A Transformation in Engineering Productivity
Welcome to the story of transformation — witness the evolution from inefficiency and overload to a paradigm of streamlined processes, faster lead time, greater flexibility and elevated productivity.
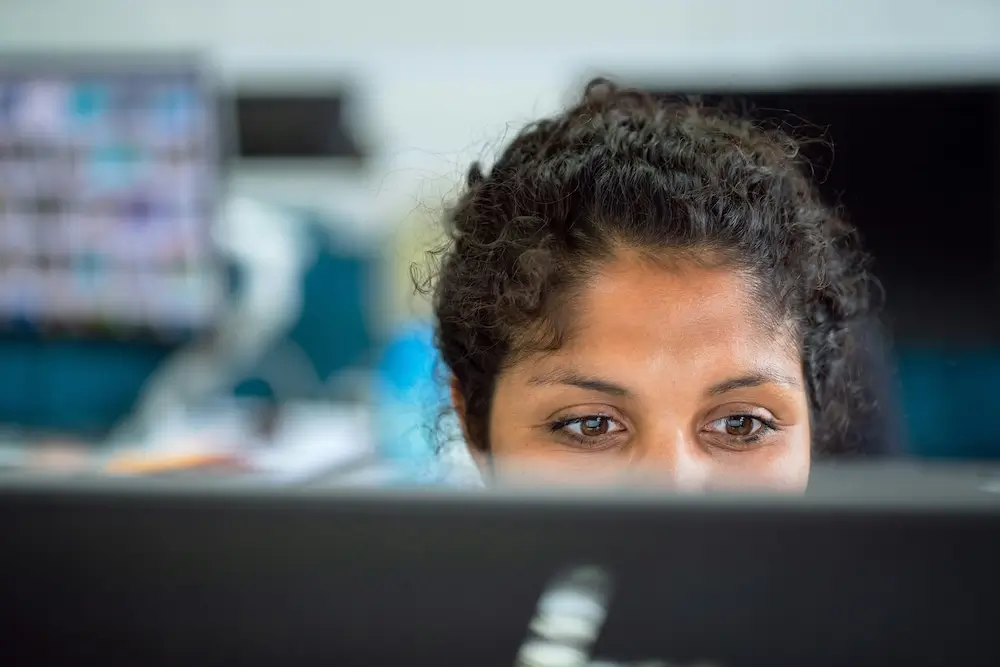
Optimising the work throughput of a Maintenance & Engineering (M&E) team was essential to increase productivity at an oil rig. The finite space capacity of the rig limited the amount of available on-site engineers, so new ways of working were required to maximise the team’s efficiency. By following the Meirik Pathway, a custom developed programme for organisational transformation, the engineering team has made a lasting change that has raised the rig’s productivity.
Operating hundreds of miles out at sea, the role of the M&E team on an oil rig is critical. Keeping equipment safely up and running in one of the world’s most hazardous environments is vital for the safety of colleagues operating on the rig. The M&E team’s work is also crucial to protect the ecology of the ocean.
Ensuring the smooth operation of the rig’s systems is their main day-to-day requirement. Rigorous procedures mean that if any potential safety issue is identified, the rig is temporarily switched off-line long before a hazard can develop. But, this impact to productivity comes at a massive cost of millions of dollars a day. This means that the ability of the M&E team to identify and prevent the escalation of any serious maintenance issues directly impacts the productivity of the rig.
The challenge
The 90 engineers who comprise the team are highly competent professionals. They were hand-picked to resolve critical engineering challenges and they have accrued experience from around the world.
But everyone is human. A creeping overflow of tasks meant that they were increasingly fighting to minimise downtime and maintain productivity. This problem also created a knock-on issue: the overburdened teams couldn’t complete larger, strategic engineering projects that could add real value – and ensure preventative measures to minimise future downtime.
The physical constraints of the rig put a limit on the number of engineers who could operate on-site at any one time, and this meant a finite amount of work that could be achieved. Internally managed efforts to increase efficiency and productivity hadn’t been successful. The organisation’s leaders knew that a deeper change was needed, but a previous attempt at change management involving a consultancy had also failed to make a tangible difference.
The Meirik Pathway
Learning of Meirik’s practical approach, the company called in the organisational transformation experts for help. The Meirik Pathway (also called Meirik Development Programme) would draw on a tailored blend of proven organisational change methods, selected to resolve the M&E team’s specific challenges.
Most importantly, the Meirik Pathway would be heavily based on on-the-job experience, where proving the solution in a live situation would validate the approach.
Operating for a defined period, after 12 months Meirik’s experts would depart. By this stage, the M&E team would have the competencies they needed to go it alone, ensuring transformation for the long-term.
Situation assessment
The M&E group comprised rig-based engineering execution teams as well as land-based engineering planning teams. Surveying the execution teams, it became apparent that they typically had insufficient time between receiving a request and its deadline. They also felt overburdened, with a higher volume of incoming work than they could complete. This situation was impacting their ability to identify and react quickly to the most critical tasks.
The overburden also meant that the execution teams deferred a significant amount of requests – especially those without a short-term priority. Not only did this add to the rising backlog, but it also prevented work on longer-term projects – projects that could help to reduce urgent maintenance issues in the long term. Tasks that required the coordination of two or more engineering teams from within the M&E division suffered in particular.
The inability to complete work projects created further problems. It wasted resources in the manufacture of specialist and costly equipment that would go used, and many of the projects were perishable, meaning that they had to be completed by a certain date or else they would have to be re-planned.
Kanban
This particular Meirik Pathway would be based on the Kanban Method. With a visual representation of tasks and workflow, Meirik selected the Kanban Method because of its fit to the team’s functional discipline structure.
A crucial first step was to understand the sources and flow of the emerging tasks. Using a customised approach to the Systems Thinking Approach to Introducing Kanban (STATIK), Meirik mapped a demand and scale chart to spot opportunities at individual team level.
The teams already had very high statistical competence, including a wide number of PhD-qualified staff. As well as aiding the task of analysis, this tailored approach was specifically geared towards the team’s analytical way of working and helped increase buy-in towards the transformation process.
The analysis clarified the excessive work demand and showed that in the case of some of the teams, they only had capacity to achieve 20% of the requested tasks. Focusing on work delivery, it also clarified the infrequency of collaboration among teams.
The Meirik Development Programme introduced a Causal Loop Diagramming (CLD) technique that the engineering team leader used to identify the relationships operating across M&E. This demonstrated that over a third of capacity was spent dealing with the reorganisation of planned projects that, ultimately, would not be completed. It also showed that insufficient request prioritisation limited the effectiveness of scheduling.
Principles of the Meirik Pathway
The Meirik Pathway set about defining principles that would guide a new process. Meirik’s experts suggested that an immediate improvement could be achieved by switching to a ‘pull’ rather than ‘push’ system of workflow. This approach would enable the engineering teams to select work based on priority, and crucially, their capacity, instead of being constrained to schedule all requested tasks.
This approach would be combined with an emphasis on the completion of individual projects, rather than a focus on maximising the amount of work in progress.
These principles would be reinforced by only allowing engineering execution teams to take 20% of the equipment resource to the rig, as opposed to the full inventory from the complete list of requested tasks.
Applying the Meirik Pathway
To put the new principles into action, the Meirik Pathway now looked towards optimising work management. Applying the key practices of the Kanban Method, Visualising the Work in Progress would describe in detail how the work would be completed, while Limiting Work in Progress would ensure the teams weren’t starting more work than they could complete.
Meirik’s experts trained every M&E team member in the practises. The counter-intuitive approach of ‘do less work to get more done’ presented resistance, including from the department’s lead. So, to ensure that the Meirik Programme became credible, and most importantly, to facilitate real transformation, introducing the approach to live situations would be a fundamental component of its success.
Meirik’s mentors introduced simulations where the teams applied the approach to real work scenarios. When every team was up-and-running independently with the Meirik Pathway, on-the-job trials could begin. At this stage, the teams were sufficiently competent in the operation of the Meirik Development Pathway to test the methods in live situations. By now, the teams also had greater confidence in the efficacy of the approach.
Kanbanize
On the rig, weather conditions didn’t lend themselves to the traditional Kanban Method of work visualisation using physical boards. The remote location of the teams and the need to manage task flow also highlighted the benefit of the Kanbanize digital variant.
Real-time digital work boards not only provided a display of metrics to chart progress, but also enabled forecasting to show with a high degree of accuracy when work could be completed.
After significant progress by each team towards completing a higher number of projects, there was still a challenge around large requests involving multiple engineering teams.
As Kanbanize gave increased workload visibility across each of the teams, it was now significantly easier to link initiatives across engineering disciplines. Each team was able to blend their workflow between single- and multi-discipline projects, while remaining within their maximum capacity. This still enabled the teams to complete their own distinct work while making progress on larger projects.
Increasing throughput
A key facilitator in the ability to increase work throughput was the strong guideline that teams should avoid reaching maximum work capacity. Previously, within the hero culture of the M&E team, there was a strong desire to try and be 100% productive. But now, managing the workload below the maximum threshold, gave greater flexibility to respond to urgent requirements. Multi-team coordination also became much smoother thanks to the increased flexibility of individual teams.
Improvements in the new way of working were also reflected in the satisfaction level of M&E team members. Even the department’s lead began wearing his ‘slack’ time as a medal of honour and emphasised his new capacity to increasingly focus on long-term, strategic projects.
Thanks to the highly analytical mindset of the team, they were able to harness the data generated through the Meirik Development Pathway to accurately map their progress. Engineering execution teams reduced their project lead times within just three months. Using this data, they could also make accurate forecasts for urgently requested tasks, based on a precise probability of completion.
Within three months, the teams achieved measurable improvements in lead times and forecasting. Productivity rose above 90%, and participants expressed confidence in reaching the 94% target soon after.
Get to know more about this initative in this Youtube video.
To learn more about how a customised Meirik Development Programme can help facilitate the organisational transformation your company needs, contact us here.